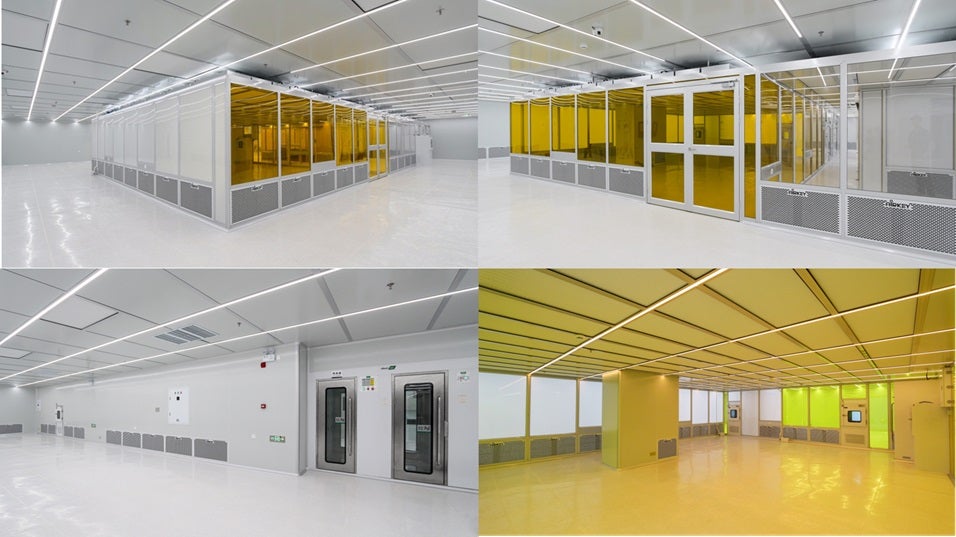
In a significant development for China’s growing optoelectronic semiconductor industry, Airkey has successfully completed a 1,000m² advanced cleanroom facility for a leading domestic manufacturer. The newly operational facility represents a major technological advancement in cleanroom design for light-sensitive semiconductor production.
The cleanroom complex features a sophisticated multi-class design with an ISO 6 (Class 1,000) background environment housing three higher-class cleanrooms for critical processes. This innovative approach allows for both large-scale production areas and ultra-clean spaces for sensitive manufacturing steps.
The ISO 6 clean rooms as a background environment incorporate several cutting-edge features:
Advanced airflow management
A key highlight of these ISO 6 modular clean rooms is the cleanroom’s double ceiling and plenum column design, which allows for efficient airflow recirculation. The double-ceiling system with air return walls creates a highly stable environment, maintaining temperature and humidity within controlled scope– critical parameters for semiconductor yield rates. In addition, the double ceilings conceal the air ducting system and water pipe system above, making the whole clean room tidier and more organised.
Precise control of temperature, humidity and differential pressure
The modular cleanrooms are designed with an HVAC system which can keep the temperature, humidity and pressure required for semiconductor production. Each clean room is equipped with a separate intelligent control panel that can monitor such parameters in real time and regulate the air velocity of each FFU individually.
In addition, the ISO 6 clean rooms as background environment are specifically made of aluminium alloy frames and 50mm and 75mm thick rock wool sandwich panels. The application of such thick mineral fibre panels leads to higher thermal insulation performance and noise insulation function, solid, stable and conductive to maintain the required temperature and humidity.
Fire safety integration
Safety has been seamlessly integrated into the design with a comprehensive, concealed fire protection system that includes early warning smoke detection, embedded sprinklers, and dedicated smoke exhaust system– all implemented in ways that minimise potential contamination risks as well as particulate generation.
Separate entrance and exit for both personnel and materials
For each modular clean room, there is an air shower for personnel entrance to remove dust attached, an air lock room for personnel exit, a buffer room and a pass box for materials entry, as well as an air lock room for finished goods exit. Such a separate entrance and exit design will effectively prevent cross-contamination, which is critical for high-class clean rooms.
In the meanwhile, the ISO 4 and ISO 5 modular cleanrooms built inside the ISO 6 clean rooms for critical production processes boast unique features:
Energy-efficient operation
ISO 4 and ISO 5 clean rooms inside adopt EC FFUs (Fan Filter Units), the use of which can provide larger air volume, enabling higher air change rate inside the cleanroom saving 20%-40% energy than AC motors. Besides, EC FFUs operate at least 10 dB quieter than AC FFUs, which makes it ideal clean rooms with such large quantity of FFUs that fully cover the modular ceilings of these large-scale clean rooms.
The ISO 4 (Class 10) and ISO 5 (Class 100) cleanrooms utilise a unique design where they draw pre-filtered air directly from the surrounding ISO 6 environment. This innovative approach reduces energy costs while maintaining exceptional cleanliness levels for critical processes.
Specialised material selection
The ISO 4 (Class 10) and ISO 5 (Class 100) cleanrooms are manufactured in modular aluminium frames with special partition wall types. There are three types of wall materials integrated into such clean rooms.
The ISO 4 modular clean room is mainly enclosed by yellow light glasses,s which are commonly used in semiconductor cleanrooms where light-sensitive processes are conducted. Yellow light glasses can filter out these harmful wavelengths, preventing unwanted exposure that could degrade or alter the photoresist materials, leading to defects in the final product.
White color acrylic panel and transparent acrylic panels are also utilized in partial areas. They are lightweight and easier for installation. White acrylic panels can protect privacy, while transparent panels with high reflectivity can enhance illumination efficiency.
The ISO 4, ISO 5, and ISO 6 clean rooms share the ESD PVC flooring. For optoelectronic and semiconductor cleanrooms, ESD PVC flooring provides the dual benefits of static protection and cleanroom-grade surface properties. making it an increasingly specified solution for advanced manufacturing environments.
Industry analysts note that this facility represents a significant step forward in cleanroom technology for China’s semiconductor sector. “As optoelectronic devices become more sophisticated, the production environments must evolve accordingly,” commented Mr. Wang, a cleanroom technology specialist. “This facility demonstrates how advanced cleanroom design can support next-generation semiconductor manufacturing.”
The project was completed on schedule despite complex technical requirements, with Airkey leveraging its extensive experience in semiconductor cleanroom construction. As optoelectronic devices become more sophisticated, the production environments must evolve accordingly, and that is what Airkey is doing now.
If you want to learn more about Airkey cleanrooms, feel free to visit our website www.airkeyx.com
Contact Airkey at inquiry@airkey.cn for further information or new projects.