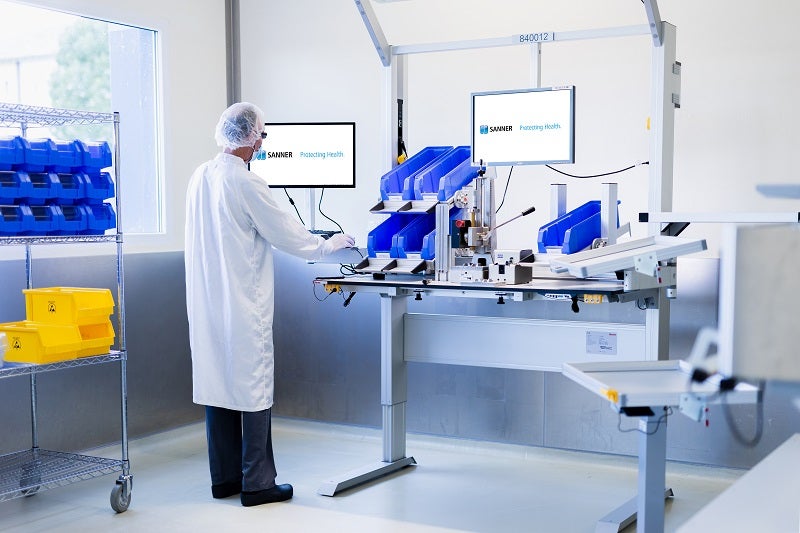
Faster workplace design and higher manufacturing competence thanks to virtual reality: The Sanner Group, a leading global supplier of high-quality intelligent packaging solutions and components for the medtech, diagnostics and pharmaceutical industries, is using VR-optimized assembly processes for the production of complex customer projects. Thanks to VR goggles, Sanner is able to virtually examine its own assembly production processes in advance and can thus optimize assembly in a resource-saving and efficient manner.
As a CDMO expert in the fields of medical technology and diagnostics, Sanner frequently develops new plastic components and medical technology products on behalf of customers. In the context of these projects, Sanner takes the lead in designing the entire product development process – from the initial idea to the design of the manufacturing system to series production and beyond. New technologies such as virtual reality are helping the company move important medical products from the design phase to industrialization more quickly.
One of Sanner’s current customer projects involves a drug delivery system: Sanner will be tasked with manufacturing the multi-part assembly unit with several chambers and assemble it, including a chip that provides dosage specifications. The project poses numerous challenges: In medical technology production, all assembly steps must meet precise specifications and be carried out with pinpoint accuracy.
The industrialization phase specified by the customer is very short – meaning that not much time should elapse between the initial development and series production. Production must be carried out in accordance with GMP guidelines in a clean room and meet ESD requirements in accordance with DIN EN 61340-5-1. In addition, spontaneous customer requirements in the early product development phase also need to be integrated into the assembly process. At the same time, it’s important to ensure the planning reliability of the results in the development phase. Virtual reality (VR) offers a new, flexible approach to the construction of assembly workstations. Together with two project partners, Sanner’s experts are reinventing their production system planning.
Less effort, shorter development time
The tailor-made VR editor solution from Halocline GmbH & Co. KG turns assembly into a virtual experience – a clear advantage over purely pictorial representation via 2D and 3D drawings. Using VR goggles, Sanner experts from Industrial Engineering can move freely in the virtual factory space as avatars and test all process sequences. This allows them to correct planning errors and inaccuracies at an early stage. It also enables them to optimize efficiency before item Industrietechnik GmbH manufactures the assembly system true to the model, thus avoiding high modification costs due to conversions at the real workplace.
Instead of haptic mock-ups, digital models from the CAD data are now used. Sanner can identify challenges in the assembly process even before they become reality; at the same time, process times can be determined and optimized in advance. With this VR-supported approach, all process steps are aligned for optimum efficiency, so that in the end, the complete assembly process is reliably defined.
Ergonomics in the workplace
Assembly workers benefit from the realistic VR test scenarios as well, as the workplace design is scrutinized from an ergonomic perspective from the outset. A virtual test reveals whether process steps put too much strain on the joints or the spine of the workers. Accordingly, work processes can be ergonomically adjusted even before the assembly table is built, for example by rearranging individual work steps or stations.
Read more information about efficient development and industrialization.