As a pioneer of containment, Powder Systems Limited (PSL) has refined a complete range of contained vessel charging solutions that will protect both the operator and the product down to nanograms containment level.
Our glovebox isolators are suitable for charging slurry and powder into reactors and other vessels from small-scale synthesis to bulk production. Many aspects have to be taken in consideration prior to design the appropriate charging solution:
- Assessment of powder transfer method and powder handling characteristics
- Evaluation of materials handling including manual or mechanically assisted requirements
- Vessel isolation method
- Assessment of pressures or steam in place requirements
SlurryBox
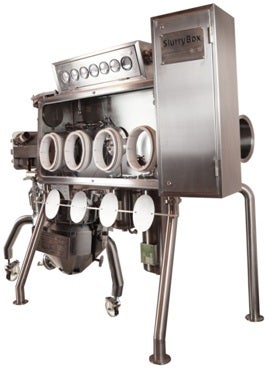
PSL recently enhanced their SlurryBox to enable charging of highly potent slurry into reactors through pressured vessels. The SlurryBox can be used as a central dispensing and weighing station servicing numerous reactors within the manufacturing site.
The vessels are specifically built for high potent process with CIP spray ring to clean each nozzle and minimum product retention design. The powder is charged safely into the vessel from the SlurryBox, and then liquid is brought in through nozzles to create the slurry. This method presents less risk of contamination with high potent powder as the product is moved within the site in a liquid state.
Finally, the slurry is directly transferred from the vessel into the reactor under pressure for a better flow control. This also avoids using valves which involve a more complexes cleaning procedure.
The facilities delivered last year also enables recovery of catalysts and carbon from the bag filter in a contained environment.
The SlurryBox achieves an OEL of less than 50ng/m³ during sampling period.
Multi-Drum Monocell
The multi-drum monocell is specifically engineered to charge a reactor from different size drums containing potent powder.
The monocell drum hoist is a pneumatic raise and lower system for multiple height adjustment with a 98° rotating actuator for a 50kg maximum lift.
The docking ring seals the drum chamber to the monocell using inflatable seals. The operator can then safely open the back door and reach into the drum without effort.
The enhanced ergonomics allows minimum manual handling from the operator.
The Multi-Drum Monocell achieves an OEL of less than 1μg/m³ 8 hours Time Weighted Average (TWA).
Contained vessel charging design features available:
- cGMP
- Systems to handle bags, drums, Rapid Transfer Ports (RTPs), split valves
- Variable drum sizes accommodated
- Drum vapour control available
- Supply of hoists and docking systems
- PSL low profile pressure-rated plug valves
- Nitrogen purge system
- Clean-in-place (CIP)and Steam-in-place (SIP) system
- Safe change HEPA filters (push-push) including remote design
- Lift up windows available for ease of maintenance
- Functional safety interlocks
- Ergonomically located display panel
- Designed according to required universal regulations
- Standard 4mm stainless steel main body construction
- Mobile designs
- Available for small-scale synthesis application