
Pharmaceutical packaging has to balance a host of complex considerations. Beyond relatively simple issues such as developing good designs and communicating with customers, pharmaceutical packagers are governed by more pressing concerns including fighting counterfeiting, encouraging patient compliance, ensuring drug integrity and balancing child-resistance and accessibility for the elderly.
This continuous series of challenges means pharmaceutical packaging firms are some of the industry’s leading innovators.
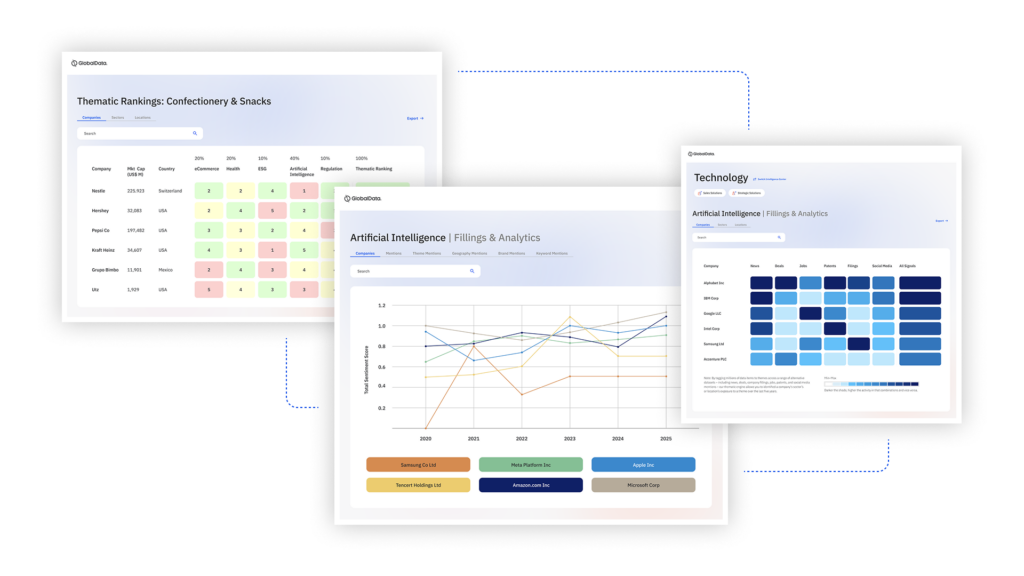
US Tariffs are shifting - will you react or anticipate?
Don’t let policy changes catch you off guard. Stay proactive with real-time data and expert analysis.
By GlobalDataHere we look at five important trends in the pharma packaging world that are encouraging designers and researchers to develop increasingly sophisticated packaging concepts.
Unit-dose packaging for greater dosage control
In recent years, the need for greater dosage control has been fuelling one of the pharmaceutical industry’s biggest growth markets: unit-dose packaging. A January 2012 study by US-based market research firm Freedonia suggests unit-dose formats, including vials, ampoules, prefillable syringes and premixed IV solutions, are some of the biggest growth drivers of the aseptic packaging market.
In fact, prefillable syringes are predicted to represent the fastest growing aseptic packaging type, with demand expected to grow 11% each year to $1.1bn.
"With more of a focus on outpatient care and the self-regulation of medicine, there’s greater onus on patients to take the right medications in the right amount," said Dow Chemical senior research scientist Jill Martin at a medical devices conference on 13 February 2012, in Anaheim, California, laying out the future trends of pharmaceutical packaging.
According to Bosch Packaging Technology, single-use dosing systems have very distinct advantages. The company has been supplying its single-use dosing systems to big pharma companies such as GlaxoSmithKline (GSK) since 2008. Only recently, the company further expanded its systems and announced it was to acquire the machinery business of Japanese pharma company Eisai – a leader in filling single medical doses.
Packaging against counterfeiting
The Food and Drug Administration (FDA) estimates that counterfeit drugs account for 10% of all medication in the US, while the EU believes between 1% and 3% of medicines sold across its member countries are fake. Clearly, these numbers endanger not only public health but also damage the global pharma industry.
Today, some of the most effective technologies to tackle counterfeiting come from the packaging industry. With technologies such as holograms, inks, dyes, tags, watermarks and track and trace technologies that use barcoding and RFID on the up, the industry hopes to keep the cost of counterfeiting low.
The latest developments are fluorescent labels, packaging with laser surface authentication, which can be identified through a unique code, and near field communication (NFC) tags.
Regulators have also taken steps to control the growing market of counterfeit drugs. In India for instance, drug companies have been sending their medicines to overseas markets including an obligatory sport barcode on their outermost packaging, starting in October 2011.
The law was enforced by the Indian Government after fake Indian medicines, originating in China, appeared in Africa. The industry has already reacted to the move and several companies, such as re-engineering company Goose, have launched trace-and-track solutions to meet the new packaging guidelines.
Non-invasive permeation testing
Barrier testing is an essential element of the pharmaceutical packaging process for products like blister packs, as it helps ensure that no oxygen has permeated the package and potentially corrupted the therapeutic within. Usually this is done either by invasive testing or time-consuming off-site methods, neither of which are ideal.
However, a new capability added to Mocon’s OpTech – O2 permeation testing system earlier this month has introduced non-invasive, non-destructive blister pack testing for flexible and rigid packaging materials – a major boon for pharma manufacturers looking to cost-effectively guarantee that their products are packaged safely.
The system now incorporates an optic sensor, which uses fluorescence to give off light that directly corresponds to the amount of oxygen present in a blister.
"Modified atmosphere can be compromised by poor packaging seals, material breakdown, weak barrier properties, pinholes, and so on," said Mocon healthcare business development manager Ed Emerson.
"This is why using a precise and sensitive package performance test method is so important – especially for drug packaging. This breakthrough technology will have a dramatic impact on how pharmaceutical companies conduct oxygen analysis.
"The OpTech – O2 system offers a simple method to quickly evaluate what is happening inside a closed blister package under real-life conditions."
Child-resistant packaging
Keeping drugs secure from young children while ensuring user-friendliness to seniors is one of the main objectives of pharmaceutical packaging companies. Child-resistant (CR) packaging was introduced in the late 1960s and early 1970s, and is most commonly known as a safety cap on bottles that has to be pushed down before being opened. More advanced CR packaging, such as special blister packs and cardboard packaging, has only been released onto the market in the last decade, and looks set to continue its growth in the future as its popularity increases.
In 2006, Stora Enso and Bosch Packaging launched Pharma small hands resistant (SHR), a re-closable and tear-resistant carton ideal for highly toxic drugs, which TestPak started using and producing the same year.
Packaging company Amcor Flexibles followed suit a few years later and introduced a CR blister pack, the Guardlid, which is compliant to CR / senior friendly (SF) regulations in Europe and the US.
Many new CR packaging concepts apply more complex and sophisticated opening mechanisms. For instance, UK packaging producer Burgopak’s sliding CR blister pack can only be opened by applying pressure at two separate points on the packaging. The blister pack and information leaflets are integrated with the outer box, which ensures the product is never separated from its packaging.
Eco-friendly pharma packaging
The pressure to develop sustainable, eco-friendly products is reverberating around the packaging industry as a whole, and has even begun to affect pharmaceutical packaging, one of the industry’s most complex sectors. The development of sustainable packaging is a balancing act for companies serving the pharmaceutical industry – environmental considerations must not lead to any compromise on a package’s safety or accessibility.
New pharmaceutical packaging concepts are beginning to emerge that address environmental concerns without sacrificing packaging advances made in the last decade. In August 2011, Keystone Folding Box Company and Legacy Pharmaceutical Packaging launched their Ecoslide-RX sustainable compliance packaging.
The pack is made from 100% recycled material, using unbleached paperboard and a clay-coated surface designed to house blister packaging with a minimum of unsustainable film and foil. The slide package meets all the modern expectations for child-resistance and accessibility for seniors, but doesn’t require heat sealing in the manufacturing process, reducing both costs and energy usage. "It is the most economical and environmentally friendly compliance packaging available today," said Keystone marketing director Ward Smith on the product’s launch.
Environmental awareness is even starting to extend to the syringe market, perhaps the most complex field of primary pharmaceutical packaging, with concepts like Cambridge Consultants’ Syreen prefilled syringe design. Syreen syringes replace glass with cyclic olefin polymer (COP), this material has allowed Cambridge to jettison secondary packaging altogether as the COP design forms its own outer shell.
The ability of packed syringes to clip into place also eliminates the need for packing materials like styrofoam and cardboard. The concept reduces packaging weight by 30% and volume by 50%, compared to standard packaging, while also incorporating anti-needlestick measures and ejectable needles so the rest of the syringe can be recycled.
By Elisabeth Fischer and Chris Lo