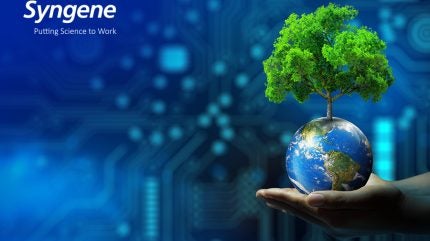
In the race to decarbonize the global economy, advanced materials are no longer a luxury – they’re a necessity. The global specialty polymer market, valued at over $87 billion globally (2024), is fast becoming the backbone of innovations in clean energy, medical devices, and high-performance electronics. Nowhere is this shift more urgent than in the green energy sector, which is forecast to surge from $119.6 billion in 2024 to $379.2 billion by 2035, growing at a CAGR of over 9.2%. At the heart of this revolution lies a deceptively simple component: the membrane.
Yet, there’s a challenge. Traditional materials have struggled to deliver the durability, efficiency, and scalability needed to power these next-gen energy systems. Performance bottlenecks in core components like membranes are slowing down green energy adoption and inflating the cost of clean energy. This is where functionalized specialty polymers – designed and synthesized to meet specific end-use requirements – are stepping in as game-changers.
That’s where tailored functional polymers come in. In a groundbreaking collaboration, Syngene’s Performance and Specialty Materials (PSM) team co-developed and scaled a specialty polymer membrane that outperformed existing benchmarks by 4x. More than a technical achievement, it’s a reimagining of what’s possible when chemistry is purpose-built. And it signals a broader evolution in how CDMOs contribute to innovation.
The Performance Imperative in Clean Energy Materials
Green energy is often touted as the fuel of the future, yet its commercial viability hinges on one pressing issue: performance parity at scale. Core components like membranes must maintain high proton conductivity, resist chemical degradation, and deliver long operational lifetimes under extreme conditions. Unfortunately, most commercially available materials falter when faced with these demands, leading to lower efficiency and increased system costs.
This gap in material capability has become a major bottleneck in the industry’s growth. According to MarketsandMarkets, the global functional polymers market is projected to grow from USD 6.1 billion in 2023 to USD 10.3 billion by 2030, at a CAGR of over 6.4%. The implication is clear: without innovation in base materials, the promise of green energy will remain out of reach.
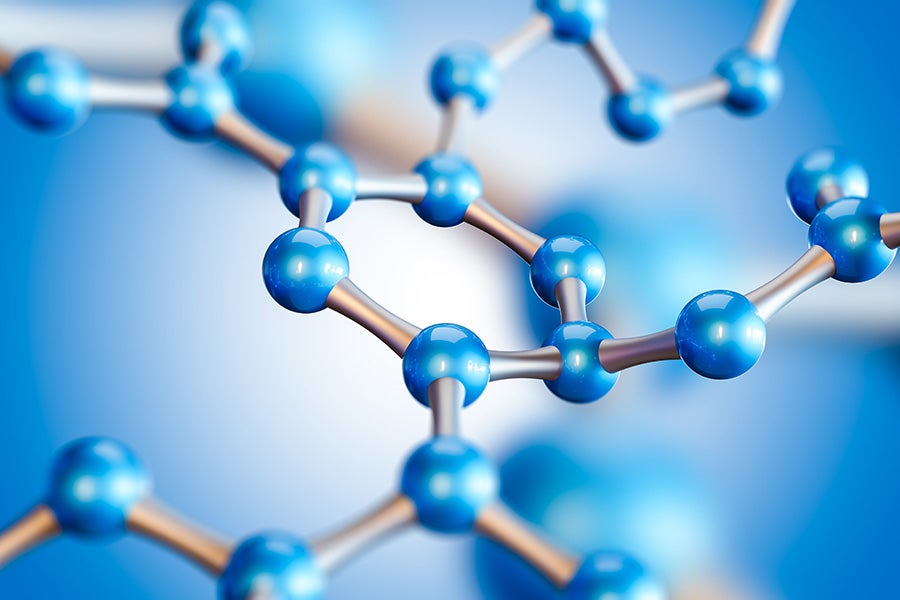
Syngene’s recent breakthrough in developing a functionalized specialty polymer that delivers 4x superior performance is not just impressive – it represents a paradigm shift. By resolving the membrane inefficiency problem, this solution makes green energy more scalable, reliable, and cost-effective.
The Role of Functionalized Polymers in Green Energy
Membranes made from functionalized polymers serve as the backbone of green energy production. Their role is crucial: they must allow selective transport while withstanding harsh chemical and electrical environments. The functionalization process involves tailoring polymer backbones with chemical groups that enhance properties such as conductivity, chemical resistance, and mechanical strength. In this case, Syngene’s polymer went beyond typical design, resulting in extraordinary membrane performance.
Globally, the specialty polymers market is valued at approximately USD 87 billion (2024), with functional polymers making up a significant and growing segment with around ~ 9%. The ability to fine-tune polymer properties is driving applications in energy, medical devices, automotive, and electronics.
From Lab Bench to Scaled Reality: A Collaborative Innovation Journey
The success of the 4x performance polymer wasn’t a fluke – it was the result of a deliberate, multi-phase R&D approach. The journey began with extensive material scouting and feasibility assessments, followed by iterative synthesis and testing. Working closely with the customer, Syngene’s PSM team optimized the structure-activity relationships to enhance the polymer’s performance.
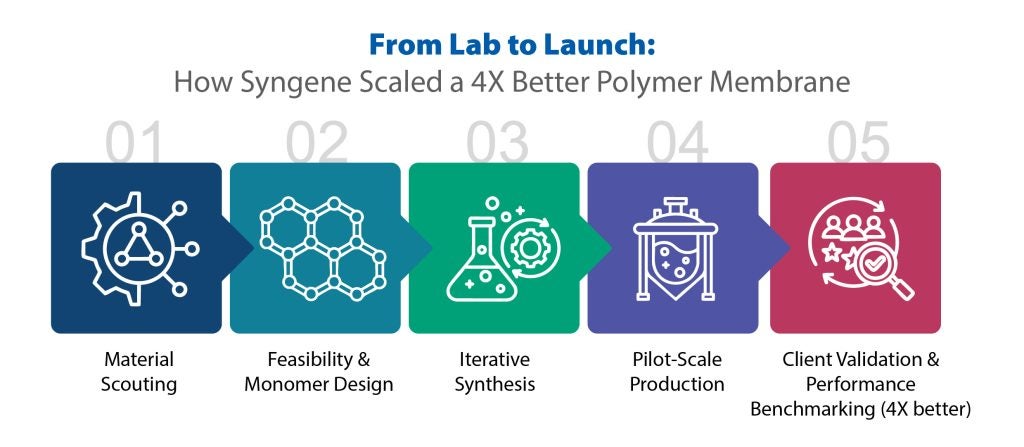
But performance in the lab is only half the battle. The team ensured process scalability from grams to multi-kilogram levels while maintaining batch-to-batch consistency. This feat required not only technical finesse but also agile project management and quality oversight to meet stringent timelines and regulatory requirements.
The Broader Implications for Specialty Materials and CDMOs
This success story is more than just a single innovation – it’s a template for how contract development and manufacturing organizations (CDMOs) can elevate their value proposition in specialty materials. Traditional CDMOs have largely focused on small molecule APIs and intermediates. However, by expanding into functional polymers and performance materials, they can unlock new opportunities in sectors like renewable energy, advanced electronics, and medical devices.
The global CDMO market for specialty and performance materials is projected to reach USD 21 billion by 2030, growing at a CAGR of around 6–8%. Players like Lonza, Evonik, WuXi AppTec have started integrating materials services into their portfolios, validating the rising demand in this segment.
Customization is the New Standard
Off-the-shelf solutions can no longer meet the needs of high-performance applications. Whether it’s the need for thermal stability, biocompatibility, or electrochemical performance, customization is now the standard. Syngene’s approach — co-designing molecules based on end-use requirements and then scaling them reliably – is proving to be a winning formula. This approach transforms polymer chemistry from a supporting function into a strategic enabler for product innovation.
The larger truth: tailored polymers are not only viable – but they are also often the only path to success in next-gen energy and device applications.
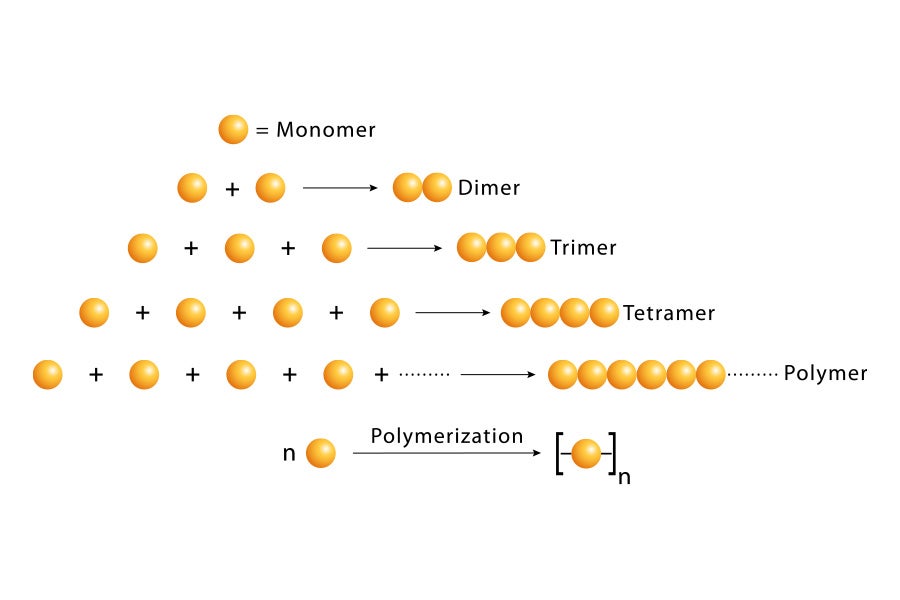
Looking Ahead: A Smart Materials Future
The breakthrough with 4x better membrane performance opens the door to even more ambitious materials R&D. The ability to tune polymers for precise function and integrate them seamlessly into real-world systems will be the hallmark of next-generation manufacturing partners.
To lead in this space, CDMOs must combine chemical design, process development, and scale-up under one roof. The future will favour those who cannot only invent new materials but bring them to market fast, at consistent quality and industrial scale.
Syngene’s capabilities – from design and synthesis to scale-up – position it as a partner of choice for clients seeking to innovate in this growing space.
Conclusion
The clean energy transition doesn’t just require new technologies – it demands new materials that can power those technologies efficiently, reliably, and at scale. Tailored functional polymers are quietly rewriting the rules of performance and redefining what’s possible.
Syngene’s polymer success story exemplifies the power of collaboration, customization, and scale in driving materials innovation for green energy. In an era where performance and sustainability must go hand-in-hand, tailored functional polymers are not just enhancing capabilities – they’re reshaping the future. As the demand for high-performance, application-specific materials grows, CDMOs that can offer end-to-end expertise in polymer development and manufacturing will be indispensable to tomorrow’s breakthroughs.