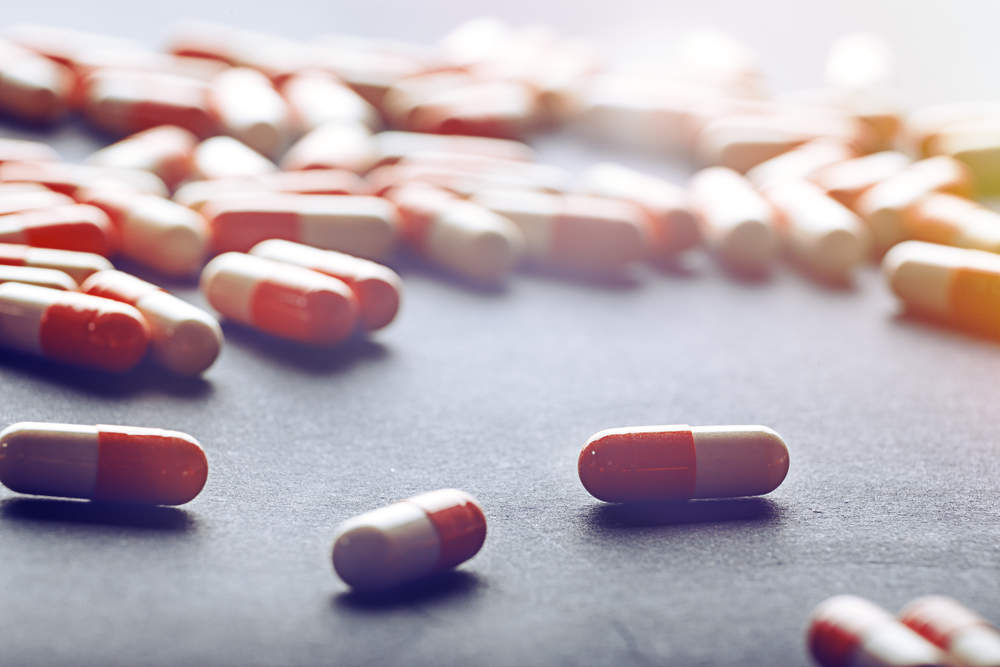
Large-scale plant shutdowns are somewhat rare in the pharmaceutical industry, given the high level of care that manufacturers must take to ensure that they comply with the rules and regulations set by agencies such as the United States Food and Drug Administration.
However, it does occur, and when it does the losses are usually significant. Plant shutdowns cost pharmaceutical companies millions of dollars and put patients at risk of complications, whether due to a lack of access to vital drugs or from side effects caused by taking tainted medicines.
Safeguarding against contamination is vital, but what are the main causes of contamination?
Employee errors
While machinery now handles large parts of the process, human operators still come into contact with machinery, materials and packaging throughout.
According to the National Sanitation Foundation, people pose the greatest risk of contamination in clean rooms. Even the cleanest of environments can become contaminated by something as minor as an unwashed hand.
It’s important that employees use adequate protective equipment to ensure that there is as little contact possible between operator and product.
ILC Dover containment solutions, such as its flexible isolators, have built in glove sleeves to allow operators to work with materials inside a contained environment without engaging in direct contact with the product.
Inadequate conditions
For employees to keep clean, it is vital that they aren’t working in unsanitary conditions. They must have access to clean toilets and adequate washing facilities.
Unsanitary conditions pose a risk during every stage of the process. Bacteria can find its way into everything from storage areas to machinery, which offers plenty of opportunities to contaminate the product.
It is important that the whole environment is kept clean at all times, not just of bacteria, but also of potential pollutants resulting from the manufacturing process. Manufacturers must ensure that there are enough vents, drains and filtration systems so that released fumes or waste doesn’t remain in the plant.
Lack of maintenance
Johnson & Johnson was forced to recall 136m bottles of child pain-relief medication Tylenol in 2010 after specks of metal were found to have contaminated the product. A McNeil Consumer Healthcare plant was force to close as a result and undergo more than $100m worth of improvements before it could resume operation.
Particles of nickel, iron and chromium found their way into the product during the manufacturing process. This was likely the result of the use of machinery that had become corroded over time through repeated use and a lack of proper maintenance.
Poor process
There are numerous ways that pharmaceutical products can become contaminated during the manufacturing process. Many of these issues relate to the cleanliness of the environment, or lack of, as well as raw materials coming into contact with external surfaces.
However, effective containment solutions can help to maintain a safe process. This can significantly reduce the chances of contamination occurring.
ILC Dover’s containment solutions keep materials safely contained inside a specially formulated film, designed to improve containment and resist contamination. This helps to ensure that the product has little opportunity to come into contact with operators or surfaces. Likewise, many ILC Dover solutions are single-use, reducing the need for an extensive clean after each use.