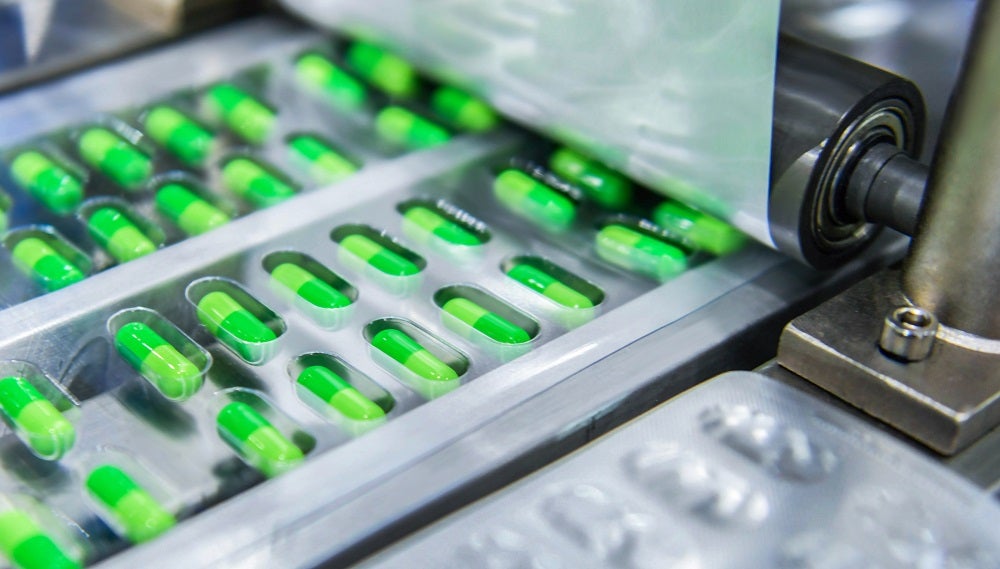
Implementing safety assurances at each stage of the development process is essential to eliminate product variants and risk. To do so, manufacturers must understand what these risks are and have good standard operating procedures (SOP) in place, as well as high-quality containment equipment.
Today, the no-observed-adverse-effect-level (NOAEL) approach, which was employed to identify the highest dose which resulted in no observed adverse effects, is often replaced with the benchmark dose (BMD) modelling approach.
BMD describes potential dose-response relationships. It has been used in a broad range of regulatory domains and industries, and typically results in more informative estimates of the doses leading to effects. Pharmaceutical manufacturers can use client-generated data for containment performance targets (CPT) and product toxicity data to set a hazard benchmark.
The increased development of materials such as cell and gene therapy products (ATMPs), antibody-drug conjugates (ADCs) and potent sterile powders mean that the handling of potent molecules in sterile environments is far more common today than it was a decade ago. Exposure limits of 1-mcg OEL would have been unheard of in the 1990s, but today these limits are into the nanograms levels.
In generic testing for containment equipment for pharmaceutical manufacturing, a CPT of 50% or 25% is often used. For nanogram level products, it is recommended to employ much stricter EN689 testing that uses 10% CPT. Eliminating product variants and risk for potent products is much more of a challenge.
ILC Dover is a containment specialist that has been increasingly approached by pharmaceutical consultancy firms and directly by customers to ascertain how to create the best environment for potent products. ILC Dover works with these companies to establish best practices for handling potent products in sterile manufacturing processes, including reviewing cleanroom setups, gowning procedures, and operator training on PPE to risk-assess the entire process.
For eliminating product variants and risk when working with potent products, ILC Dover recommends several standard review points before developing safety assurances. These include having a grade in the isolator (sterility testing), asking where you can separate the operators from the process (such as utilising mechanical controls), changing gowning procedures, considering a decontamination procedure, updating PPE, and providing additional environmental monitoring.
Developing a good SOP entails understanding all the application requirements and providing all operators with procedures that they can follow, regardless of their experience and level of seniority. Not only is it important that manufacturers utilise the right equipment, it is imperative that operators understand how to use it properly at every stage of the development process.
As world-leading experts in the design and production of engineered flexible solutions for the pharmaceutical and biopharmaceutical industries, ILC Dover offers a range of containment equipment suitable for eliminating product variants and mitigating risk. Download the whitepaper below to find out more about ILC Dover’s flexible solutions for protecting the entire value chain.