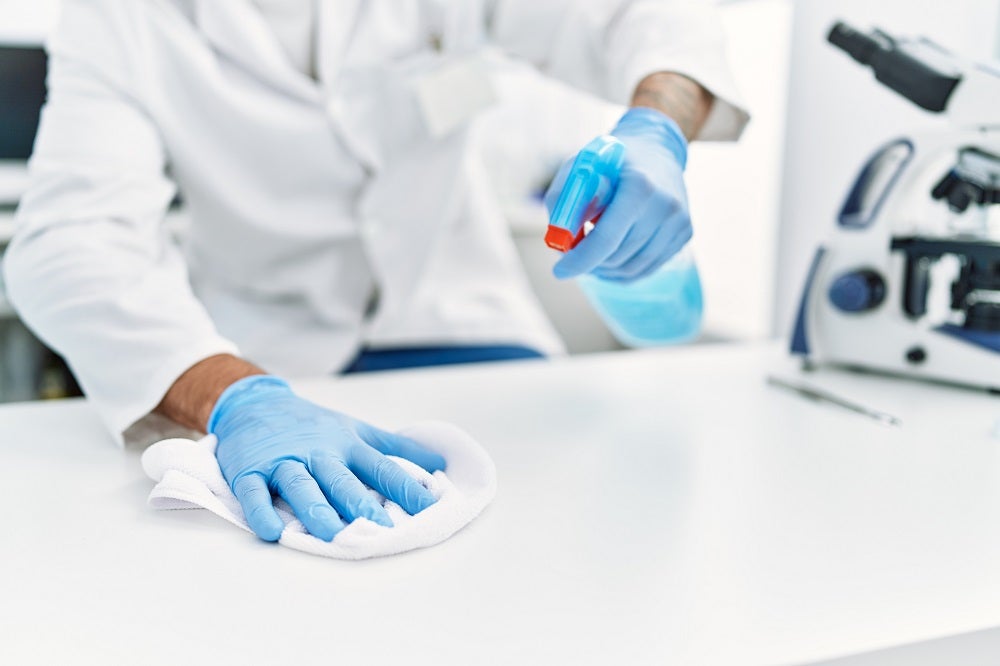
Cleaning and disinfecting pharmaceutical isolators is a laborious task, and one that will only get more difficult as the industry increasingly handles potent powders.
The EU GMP Annex 1 Revision: Manufacture of Sterile Medicinal Products, updated in 2020, outlines a need for cleaning processes to be validated to remove any residue that could impact effectiveness, as well as minimise the risk of cross-contamination. For manual cleaning procedures, validation requires that strict cleaning procedures are followed and that the environment is monitored before and after disinfection.
Pharmaceutical isolators are typically going to require Grade A cleanliness levels outlined by GMP standards or meet the equivalent ISO 5 requirements. These stringent cleaning necessities can disrupt workflow and slow down output, so facility restraints and closed-barrier systems need a better way to handle sterile potent powders.
Single-use handling and gamma-irradiation sterilisation
ILC Dover brings one such solution to the table in the form of its fully disposable, single-use chamber and CAPEX-efficient soloPURE. Introduced in 2021, this flexible aseptic isolator is a cost-effective, closed-barrier system for sterile manufacturing.
In a webinar introducing the new isolator design, Martyn Ryder, business and product development manager at SOLO Containment and ILC Dover says: “We believe this single-use aseptic isolator could completely transform aseptic processes, especially for small-batch manufacturing.”
Ryder explains that the system was designed to handle high potency aseptic powders, and offers a much more rapid delivery system than traditional technology. Additionally, this flexible solution is upgradable, so is agile for future developments.
soloPURE is a mobile isolator with a small footprint, and provides a closed, Grade-A, aseptic environment for fill and finish activities. The fully disposable chamber maximises productivity and cleanroom efficiency and enhances operator access with double-sided entry. Integrity testing throughout the system’s lifecycle enables facilities to mitigate risk.
In the webinar, Declan O’Shea, technical sales manager at ILC Dover LP explains: “Single-use handling of potent powders avoids cross-contamination and cleaning issues, a disposable system is highly beneficial. Alongside that, we also provide a VHP system as an alternative in the same design.”
This new technology has the capability to sterilise in-place with VHP or operate with the disposable gamma-irradiated chamber. The VHP system enables facilities to attach heavy equipment such as semi-automated filling devices.
“We have designed this system so it can operate in both positive and negative pressure,” O’Shea explains. “The reason for this is that primarily with an aseptic unit you would associate it with a positively pressured system, however when you’re working with a potent powder, you’ll probably want to look towards a negative pressure system.”
soloPURE is FDA Sterile Manufacturing and EU GMP Annex 1 compliant and offers H14 HEPA air supply filtration, as well as an ISO 5/Grade A particle count upon start up.
Overall, soloPURE maximises efficiency and productivity with its small footprint and automatic control system, as well as eliminating cleaning validation requirements when using the single-use chamber. It reduces cost and delivery time with lower capital expenditure costs and shorter lead times, as well as making it much easier for facilities to mitigate risk and meet regulatory compliance.
For more information, download the whitepaper below or watch the full webinar here.