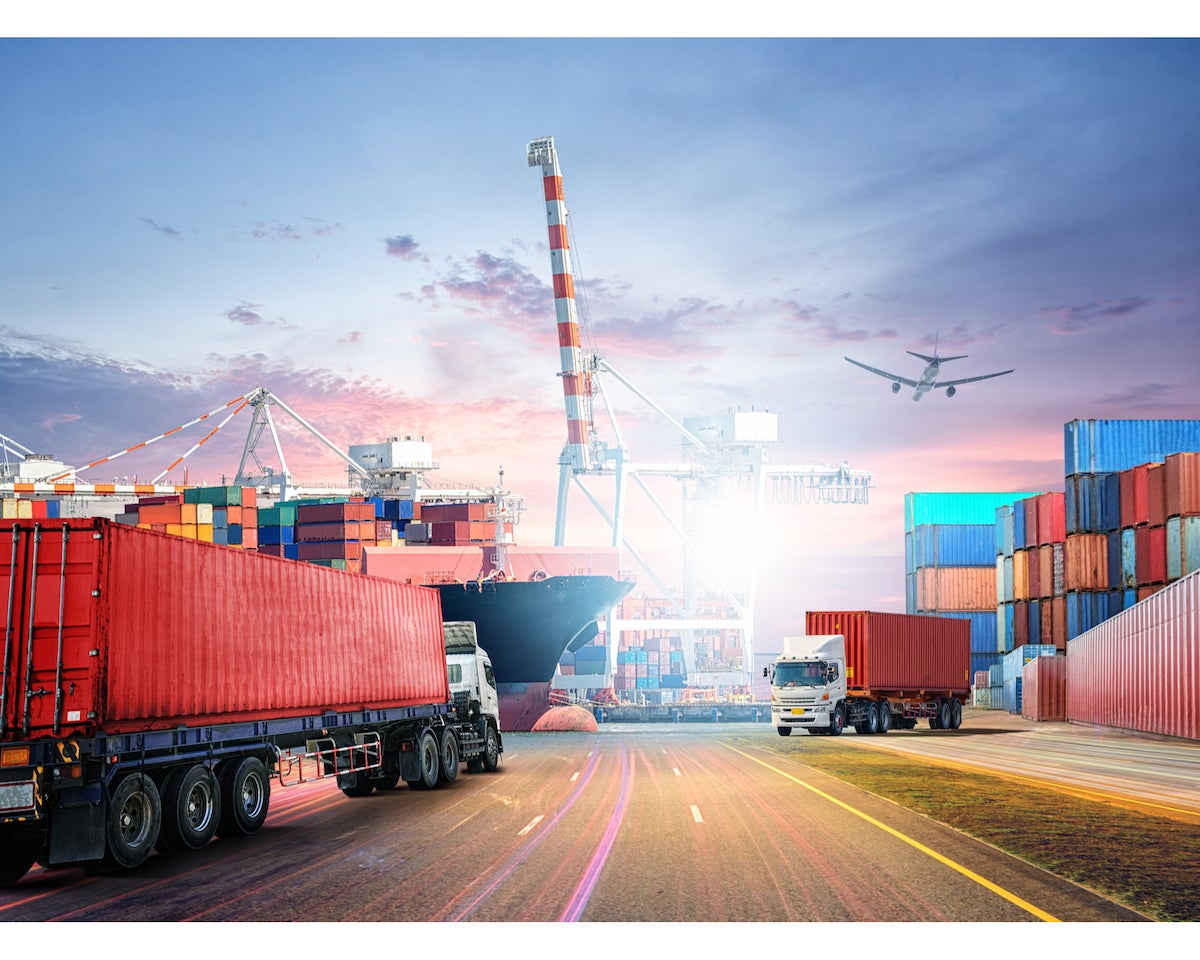
Like most industries, the pharmaceutical market (including specialty logistics) has changed dramatically over the past few decades, with manufacturers now increasingly focusing on developing patient-centric strategies for their treatments – even more so now with the onset of the COVID-19 pandemic. Operating a supply chain under new tighter restrictions has led to a surge in direct-to-patient (DTP) shipping. Transitioning to this logistics model requires thoughtful consideration from conception to delivery of your treatments.
Because of the pandemic, there are simply fewer shipping options available to pharma companies and biotechs – there are fewer planes in the sky, customs strictures and routines have become far more complex. And with DTP being the continuing trend, shipments are now, more than ever before, either more time-consuming, more costly, or both. And that means shipment failure is becoming more likely at a time where making sure your treatments get to your patients has never been more critical.
Pharmaceutical Technology spoke with global logistics specialist World Courier to talk about the reasons shipments fail and how they’re solving these problems for their customers.
“There could be a number of factors that go into shipment failures and in 2020, the complexity of moving treatments around the world has only increased,” said Nils Markmann, VP of global operations at the London-headquartered firm. “Because of this, most companies are closely examining every link in their supply chain and focusing minutely on maximising shipment delivery rates”
Markmann is right – expanding supply chain complexity, growing global regulatory pressures and increased security and data requirements means biotechs and pharma companies run the risk of shipment excursions becoming more likely. Losing patient good will, possibly endangering life or losing contracts to competitors means that every advantage must be taken –where once the argument was whether to use a general or specialty logistics partner, now it’s not even a question.
Specialty logistics has increased
“Today’s pharmaceutical environment has become increasingly complex, with more specialty products like biologics, injectables, and clinical trial drugs being shipped than ever,” Markmann explains. “The logistics industry standard for commercial packaging is 120 hours, which is no longer always adequate. Better temperature control and the right packaging are essential to keeping product integrity intact.”
The other thing to consider when choosing a specialist logistics partner is that many manufacturers have responded to the economic downturn and the rising expense of drug development by establishing clinical trials in emerging markets.
This brings its own challenges, especially around the logistics of transporting these new, incredibly delicate treatments. Temperature sensitivity and short shelf lives require absolute precision in delivery. Excursions could not only cost vast sums, but put the viability of treatments at risk and ultimately affect the lives of patients. The stakes, then, are high. All of which puts your procurement and logistics teams under unprecedented pressure. Especially as patients and production facilities are now more geographically dispersed.
World Courier solves this, says Markmann, by having its storage and distribution depots strategically located around the world in key markets. Having a globally owned network ensures treatments follow the same quality standards wherever they travel.
For example, the company has helped dispatch biological samples from remote villages in southern Bangladesh and urban hospitals in post-Ebola Liberia, via sub-zero conditions, to scientific partners in Europe and the United States for analysis – an impressive feat with the worldwide logistics slow down.
Can you better predict the risk of incident in the delivery of your shipment? View the whitepaper below to understand how you can calculate the dependability and risk factor of your supply chain.