
Industry 4.0 is revolutionising global manufacturing, driving industries like medtech towards larger machines, faster production processes, and smarter, more connected systems. And this transformation – encompassing processes as divergent as tooling and simulation – is particularly evident in autoinjectors.
Combination products have shifted away from resource-intensive bespoke designs to embrace more efficient modular, platform-based manufacturing. SHL Medical’s DAI® technology was one of the first autoinjectors to explore a platform design model, which features a recognisable industrial design for various diseases. Modularisation has since improved scalability further as shown by SHL Medical’s Molly® autoinjector, which has supported the approval of at least 17 distinct combination product projects across diverse disease areas.
With pharma companies striving to address a widening range of diseases through novel drugs and biosimilars in autoinjectors, efficiency is an even more critical competitive edge for medical device makers.
Simulating operations to stimulate efficiency
Christian Walter, Global Head of Operations Engineering at SHL Medical, says the company has been expanding and accelerating its manufacturing operations for several years now by leveraging Industry 4.0 technologies, such as end-to-end process digitalisation, in-house automation, and extensive data analytics for scalable production.
To facilitate this expansion, a critical step SHL Medical has taken is applying advanced simulation methods and tools to create virtual models of its processes, production lines, machines, and supply chains.
“Simulation is a powerful technology that’s transforming how we assess and optimise complex processes,” he says. “It lets us dive into individual processes and understand how they interact. Executing multiple simulation events in a virtual environment gives manufacturers the insight needed to make informed decisions about their operations.”
Walter adds that simulation technologies are ideally suited for autoinjector production, citing the complex processes, well-defined supply chains, and numerous system constraints involved.
What does simulation look like in practice?
SHL Medical, as an end-to-end solutions provider, has a dedicated team of plant simulation engineers, who use advanced modelling techniques to simulate the processes behind an autoinjector’s production. The team employs simple static models and highly integrated, dynamic simulation modelling, depending on the requirements of the simulation task.
Static modelling, Walter says, is a straightforward but effective way to create multiple scenarios and rule out inadequate solutions. “For instance, we can easily assess production quantities, throughputs, and space constraints,” he explains. “By inputting the right data and formulas, a plant simulation engineer can quickly establish various production settings, consider average and worst-case scenarios, and determine the ideal setup.”
Simulation modelling is a more visual and advanced technique in which engineers use specialised software to create sophisticated discrete-event simulations. These animated representations of complex systems enable the study of dynamic interactions among multiple processes and subsystems.
SHL Medical has applied simulation modelling extensively, creating modularised 3D models of its entire manufacturing infrastructure. This allows for the simulation of discrete and continuous manufacturing processes across its global facilities, production processes, material flows, and automated machinery.
The highly demand-driven process of managing production capacities across multiple autoinjector platforms requires a continuous optimisation of material flow, resource utilisation, and various other dimensions.
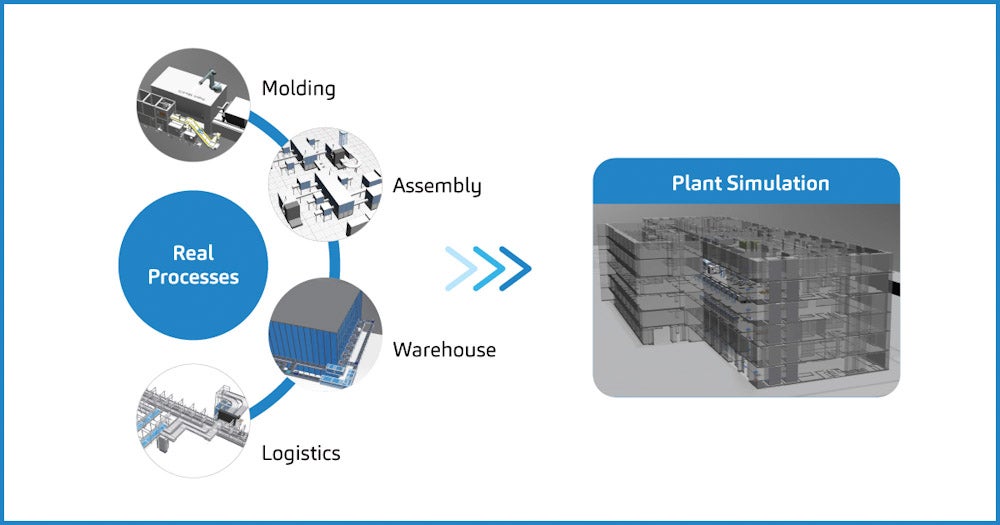
Plant simulation on the production floor
For pharma companies in a constant race to reduce time-to-market, simulation’s biggest advantage is accelerating lead times from device makers. In the case of SHL Medical, both new and existing projects benefit from the plant simulation team’s effort to dynamically analyse opportunities for process improvement and optimisation in real time.
“Through an internal request management system, any function at SHL can inquire and investigate optimisation proposals for specific production processes or operational flows,” Walter says. “And because we have a highly diverse process landscape that utilises production machinery of varying levels of automation, analysing the interactions between the people, machines, and production layout can yield big benefits in maximising operational efficiency.”
Plant simulation is essential for throughput modelling and optimisation. For example, in a hypothetical scenario, initial production components move from the material distribution station to a buffer area before assembly in the Fully Automated Assembly Machine (FAAM). This simulation assesses the trade-off between a lean, cost-effective workforce and a larger workforce in terms of material replenishment. SHL Medical uses this granular analysis to identify the optimal balance for efficiency in various scenarios.
Facilitating a global expansion
As the number of patients who rely on autoinjectors for treatment continues to surge, SHL Medical has also found simulation to be helpful at a much larger scale.
The company is currently undertaking a global expansion, with new manufacturing sites under development in the US and Switzerland. These sites will bring production lines closer to the headquarters of many industry-leading pharma and biotech companies, and together with SHL Medical’s existing Taiwan facility, embodies the true essence of 24/7 operations.
“The simulation team has modelled the operation of each factory, from the process flow to material handling to machine interaction,” Walter says. “Our aim is to implement equivalent operating models across all sites, whereas there are significant differences in terms of layout of each facility. This means our simulation models – whether for the machines, shop floors, or spaces – can be leveraged across all sites.
“This is like stepping on the accelerator for SHL Medical’s expansion, as we won’t have to spend time and resources planning the operations of every new facility from scratch.”
With mass customisation forecasted to be the next trend in autoinjectors, simulation appears set to be a vital component in achieving the manufacturing flexibility and scalability needed to meet the needs of pharma companies and patients.
To learn more about SHL Medical’s Molly® modular platform autoinjector, download the document below.