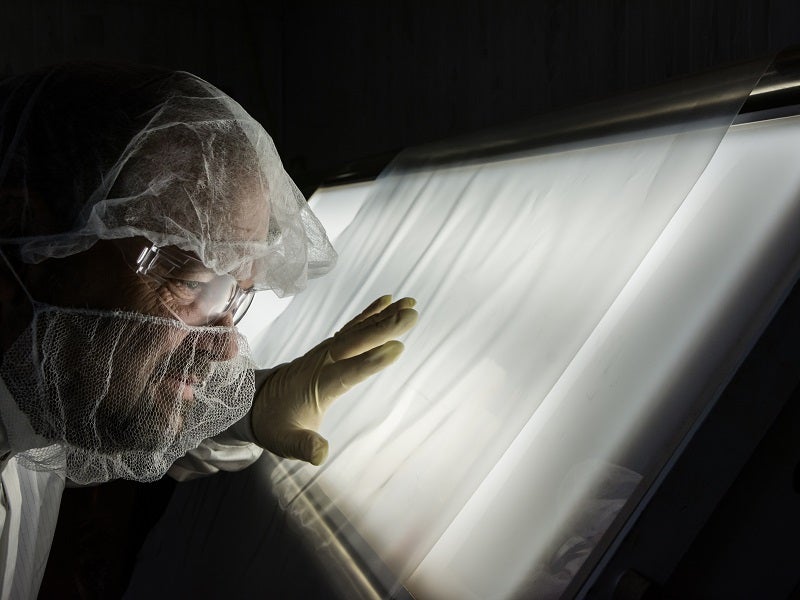
Maintaining the integrity of a drug during a pharmaceutical manufacturing scale-up isn’t always an easy feat, but it’s essential for producers who wish to grow their operation while ensuring high standards and legal compliance.
In the transition from phase 1 to manufacturing, operators may need to scale up their operation several times over, each time making sure they set themselves safe and realistic goals. A successful product may go through the scaling process several times during its commercial life.
Most small-scale cell growth is done using small bottles of media and buffers. As processes are scaled up to a manufacturing level liquids get expensive to ship and store and are no longer a viable option, and instead powdered media and buffers are brought in.
Powder handling at larger scales is increasingly being recognised as a new headache to manage because it completely changes the whole process. In order to do this new single use technologies that were not part of the original smaller scope need to be validated. The main concerns are making sure the powder isn’t getting into places where it shouldn’t go and becomes a contamination risk. The single use solutions also need to be ergonomic and safe for the users.
One of the leaders in single use powder handling is ILC Dover whose powder handling products are designed to be compatible with pharma manufacturing operations of numerous capacities. With over 300,000 successful product installations across the globe, pharmaceutical and biopharmaceutical companies rely on ILC Dover for their powder transfer systems every day, from cGMP to nanogram levels.
Contamination
One of the biggest concerns pharmaceutical manufacturers have when transitioning from a small-scale to a large scale operation is that they face a higher risk of product contamination as they get to grips with new processes.
To minimise contamination risk, the entire pharmaceutical processing system must be closed. ILC Dover’s single and multiple-use containment systems keep powdered materials contained inside a specially formulated film. This way, the product is significantly less likely to come into contact with foreign contaminants.
Single-use solutions are also beneficial as they can be disposed of after each use. This minimises time wasted on cleaning validations, weigh and dispense steps, and concerns about powder contaminations.
Regulation, regulation, regulation
It’s also important to be aware of regulatory considerations. For example, before any US-based production unit scales up its operation, it must follow the Food and Drug Administration (FDA) sanctioned Scale-up and Post-Approval Changes (SUPAC).
The entire scale-up process must be validated in line with SUPAC guidelines every time it grows by a factor of at least 10. This process requires making either a Prescription New Drug Application (NDA) or an Abbreviated New Drug Application (ANDA), depending on the nature and requirements of a product. If the scale up is immediate, Prior Approval Statement (PAS) may need to be filed.
Different jurisdictions will have different guidelines, so pharma manufactures must make sure they have assessed theirs and are ready and able to comply before purchasing any new equipment.