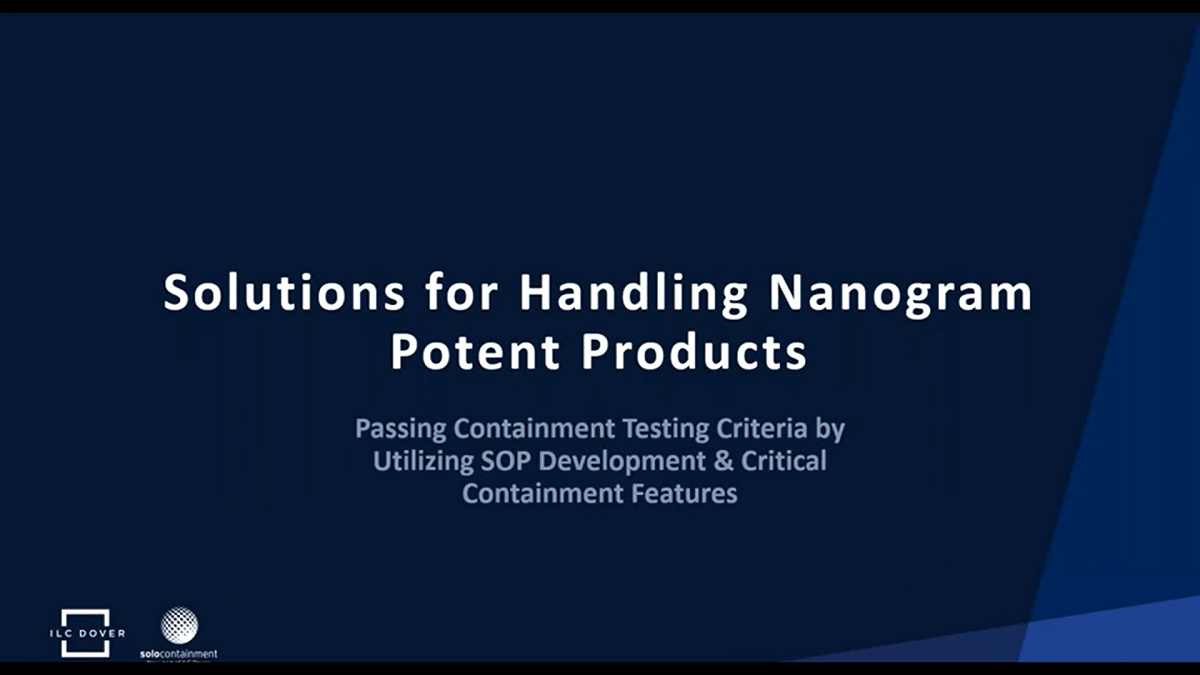
As innovative research into more targeted therapy continues to develop, the handling of potent molecules has been on the rise. Over the past decade, 1µg/m3 has become the new normal, and as the industry moves towards nanogram level potent products, containment systems must evolve in tandem.
ILC Dover engineers and manufacturers flexible containment technologies across a broad scope of industries and processes, from pharmaceuticals to aerospace applications. With experience handling a broad range of products, ILC Dover is ideally positioned to support customers with even the most potent products.
In a webinar titled Solutions for Handling Nanogram Level Potent Products to Pass Containment Testing Criteria, product manager Declan O’Shea explains how mechanical controls and a good standard operating procedure (SOP) can help you to pass containment testing criteria for your isolator.
What is containment testing?
“One thing we get asked a lot is if containment testing is mandatory,” O’Shea explains. “There’s no overarching regulatory body that will say you that you must test an isolator, however, it is highly advised. If you are running a highly potent process where you feel that there is a risk to the operator, then we would advise that you perform a containment test of some sort.”
Performing and passing a containment test guarantees the functionality of your facility and provides reassurance for the supply chain. It is also attractive to potential customers, as it proves your capabilities.
A key benefit that should also not be overlooked is the reassurance that testing provides to operators. All too often, operators have uncertainty before beginning a process, which is particularly problematic when dealing with nanogram level potent products.
Depending on the product, there are a number of variations when it comes to testing methods and how strict the criteria is. According to O’Shea: “In most generic tests, you’re looking at 50% or 25% containment performance target (CPT). If you want an isolator to perform to 1µg with a 50% CPT, then you are looking at 0.5 CPT. What that generally means, is that none of the results that you gain go over your target value, but the mean of your samples will not exceed your CPT value.”
For nanogram level products, O’Shea recommends EN689 testing, which is much stricter. This involves 10% CPT, three diverse operators (such as various levels of experience), and three runs. Using its isolators recommended for nanogram potency, ILC Dover equipment has been able to pass these strict tests with excellent results.
“The golden rule is to simulate your process as close to real-life circumstances as you can,” O’Shea adds. “You don’t want to look at doing this in a different room with different people with a different process just to pass your results.”
When carrying out testing, companies also need to consider whether to collect air or surface samples, and which locations they with gather these samples from. For nanogram level potent products, it is recommended to collect both air and surface samples from at least the key areas; on the operator, as well as at entry and exit methods.
The best way to make an informed decision about sampling methods and what surrogate to use during testing is to utilise a risk assessment. Where in the process is contamination or exposure the greater risk? Once this is ascertained, companies can focus on what areas requires the most testing.
Mechanical controls and SOP development
According to O’Shea: “Mechanical controls are great for mitigating risk and should always be considered as the primary and preferred solution. Anything that you don’t implement mechanically, you must implement from an operator interface perspective. So, while the capital investment may be high for the equipment, you have to consider the ease on the operator process for however many years you intend to run this. You might actually see a saving by investing in mechanical control.
“Developing an SOP around product handing and interfacing with equipment is extremely important, so you can bridge that gap in the elements of risk that you can foresee with your process. Consider what is in and out of control for your operator, because if it’s not within the operator’s control then we must find the mechanical means to overcome that.”
Mechanical controls such as automation increase the practicability of processes and have a proven track record of safety, making them idea for applications such as safe entry and exit materials, as well as removing waste, which is often the biggest failure when it comes to contamination.
Alongside these mechanical controls, companies need a good SOP. This includes providing clarity to operators with detailed information about processes (ideally with diagrams and visual aids). Not only does this provide reassurance to current operators, but it grants clarity to future operators and those who may have less experience. A good SOP must also take human error into account and have plans in place for corrective action.
“We have the experience in conducting these tests and working with our equipment, no one knows our equipment better than we do,” O’Shea states. “We help with SOP development and formulating the best mechanical controls in order to really provide a system that is going to work for our customers.”
For more information, download the whitepaper below.