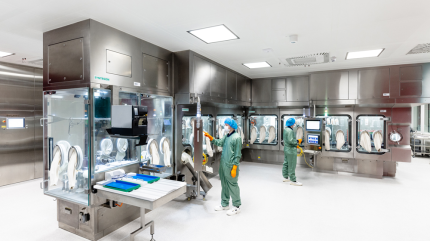
The rise in the production of biologics and complex pharmaceuticals is driving the need for advanced aseptic processing technologies that are capable of handling large-scale production. The prevalence of chronic illnesses, such as diabetes and autoimmune disorders, is also increasing the demand for injectable medications.
This trend necessitates expanded manufacturing capacity for injectable drugs, particularly those that require aseptic conditions. Indeed, the global market for pharmaceutical glass vials (an indicator of aseptic processing) is projected to grow significantly, from $12.1 billion in 2023 to $24.1 billion by 2033, suggesting a robust demand for aseptic manufacturing solutions[i]. As a result, some commercial isolator lines are now capable of producing hundreds of thousands of vials per batch.
Isolators are specialised enclosures designed to create a controlled manufacturing environment for drug products, ensuring a sterile environment for filling and stoppering operations, protecting drug products from environmental contaminants and workers from hazardous materials, especially when working with pathogens with high biosafety levels.
This is achieved by separating the human operator, often considered the main source of potential contamination, from the open process, with any manual tasks necessary performed using glove ports. Commercial isolator lines systems also facilitate automatic loading and unloading of equipment, reducing the need for operators, and isolators have their own air supply with Class A clean areas dedicated to high-risk operations such as fill/finish, open ampoules, vials and making sterile fluid transfers.
Isolator lines are invaluable for large-scale pharma manufacturing with increased automation of manufacturing processes and longer run times, increasing efficiency and reducing costs.
Key challenges for isolator lines
Marcel Langner is a pharmaceutical engineer and Head of Manufacturing for IDT Biologika’s high-speed aseptic filling line. IDT Biologika is one of the world’s leading CDMO’s for end-to-end services in manufacturing recombinant proteins, viral vectors, virus-like particles, oncolytic viruses, monoclonal antibodies and biosimilars.
When implementing a new filling line, a key challenge is the utilities and the surrounding facility, which must fulfil certain requirements. “Such lines fill at an extremely high speed, which needs to be considered with regard to media supply (e.g. water) and material delivery,” says Langner. “The supply process for realising a process and the need for storage areas for additional equipment are often underestimated.”
Another common issue faced by the pharma industry today is a shortage of skilled professionals, leading to high turnover rates and increased operating costs as companies struggle to fill positions with qualified candidates. Isolator lines are no exception, says Langner. “Recruiting, training and qualification processes need to be adequately implemented. Isolator lines run 24/7 making operator availability a prerequisite, and the operating/control system of the line and the isolator, needs to be set up correctly,” he says.
Advantages of automation
According to Langner, some of these issues can be solved through the innovative use of automation, which also reduces the need for the operator to manually intervene and risk contamination. “Automation aims to maximise output with high quality measures, while still allowing 100% control over each vial used before filling. Ensuring 100% control over filling weight and the presence and position of all stoppers and caps. This ensures maximum output and quality control.”
Isolator lines can significantly enhance production efficiency, Langner explains, due to their ability to remain sterile during filling processes: “Isolator filling lines are especially suited to produce individual products in large quantities. Prior to routine productions, a defined production time (holding time) for the isolator is determined, meaning the longest proven time without any contamination.
“Within that time, production can constantly be performed with the same risk level. Without such a strict separation of the filling line, the holding time is significantly reduced, as the operators increase the risk of contamination the longer the process runs. Consequently, risk minimising actions – such as cleaning, disinfection and down time for room recovery – needs to be regularly repeated. Therefore, using isolator filling lines, higher quantities can be produced in less time.”
One example for this is the production of the Dengue vaccine by IDT Biologika. “As isolator filling lines are extremely efficient for producing large quantities of product, an existing manufacturing process can be upscaled by adjusting the formulation process.”
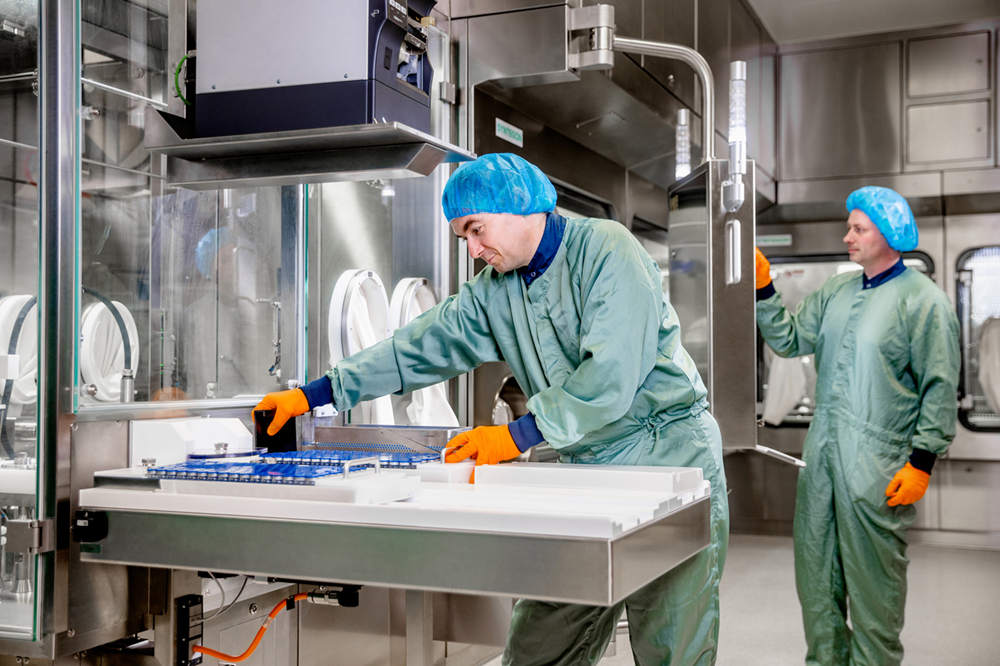
Working with customers to provide end-to-end services
IDT Biologika has over 100 years of expertise in biologics, with a focus on delivering its customers’ products with the highest quality and maximum flexibility. Scalable solutions in process development, drug substance manufacturing (from 200 to 2000L), aseptic fill-finish and packaging ensure a smooth and efficient process transfer means leveraging its deep expertise and proven platform technologies. All manufacturing processes are supported by in-house analytical services.
Cost efficient, tailored and high value service offeringto meet diverse modality and production needs, as well as consistency and quality at every scale, with full GMP compliance – these are the company’s outstanding features. “From early process development to clinical and commercial manufacturing, we provide seamless integration at every step of the process, ensuring flexibility, uncompromising quality and regulatory compliance,” says Langner. “With expert insights and collaborative mindset our dedicated team creates tailored solutions that enable our customers to enhance their products and address the evolving demands of global healthcare.”
Looking forward, Langner says that IDT Biologika now runs two high speed isolator filling lines for commercial use, and with this manufacturing capacity, can play a significant role in providing aseptic products. The newest line is one of the fastest in the world and can serve up to 100 million vials per year. With batch sizes of up to 500,000 vials each, its own air ventilation system (including return air filtration), and H2 O2 decontamination and inactivation it is supported by a fully automated visual inspection unit.
[i] https://www.glass-international.com/news/bormioli-pharma-reports-north-american-glass-success