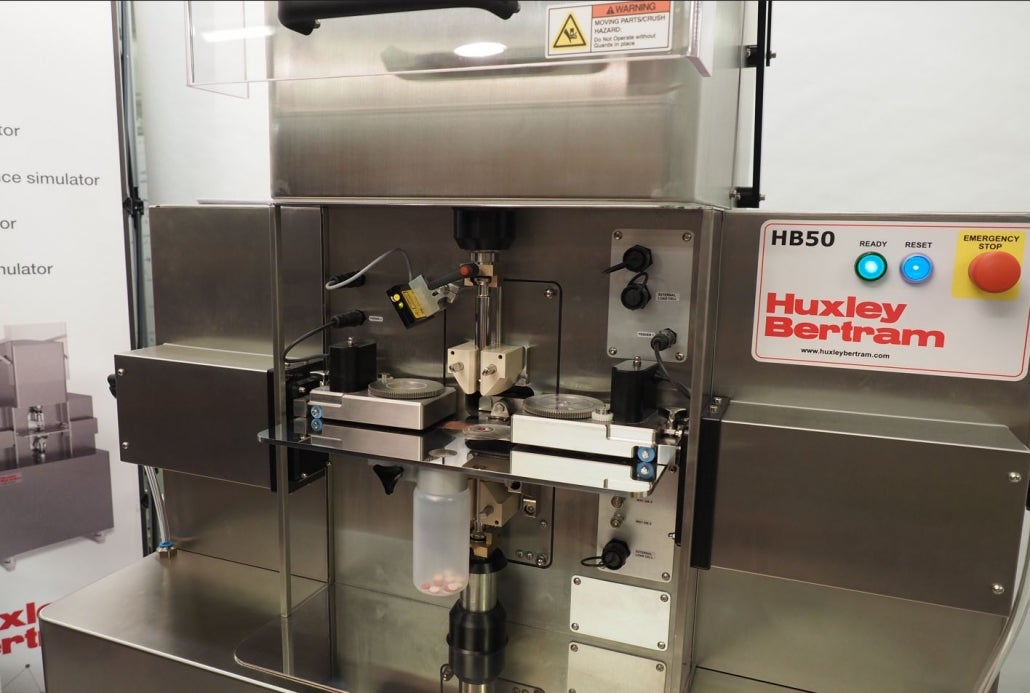
Founded in December 2020, CMAC and Huxley Bertram established the Compaction Simulation Pilot Test Facility providing Compaction Simulation Research Services through CMAC’s National Facility team. The Compaction Simulation Test Facility and services have proved to have been very successful throughout 2021 and 2022. The offering is unique with the support of analytical services, available to the CMAC team.
The initiative is supported by the partnership between HuxleyBertram and the CMAC Future Manufacturing Research Hub, based at the University of Strathclyde (Glasgow, UK). An HB50 Huxley Bertram Tablet Compaction Simulator specified with instrumented dies and innovative process analytics for in-situ measurements using terahertz spectroscopy has been installed at CMAC’s facilities. Compaction simulation research is being led by academics and scientists at CMAC, with expertise in compaction simulation. With cutting-edge application and engineering support provided by Huxley Bertram’s Cambridge-based staff.
Compaction Simulation Services
Varying levels of Compaction Simulation services and development are available on a contract basis:
- Material characterisation and advanced compaction studies of active pharmaceutical ingredients (APIs), excipients, and blends
- Routine powder characterisation, constitutive analysis (axial stress/strain)
- Compatibility, compressibility and tabletability studies
- Radial analysis (instrumented dice)
- Advanced compaction studies: radial analysis, frictionless ejection
- Die compaction (rotary press) roll compaction and capsule tamping
- High-fidelity rotary presses simulation, including hybrid MODUL simulations
- Material-sparing replication of direct compression and dry granulation processes (DC/DG)
- Formulation assistance and optimisation including lubrication studies
- Formulation design, development and scale-up
Process Understanding Development
- Compaction and materials science understanding by pairing compaction simulation with advised characterisation techniques: X-ray computed nanotomography, time-of-flight secondary ion mass spectrometry
- Compaction thermodynamics, in-die temperature evolution
- Microstructure analysis using terahertz spectroscopy and x-ray computer nanotomography
- Troubleshooting of clinical and commercial die compaction processes
For further information regarding the range of Tablet Compaction Simulators, which include containment options, please contact us
14 September 2022