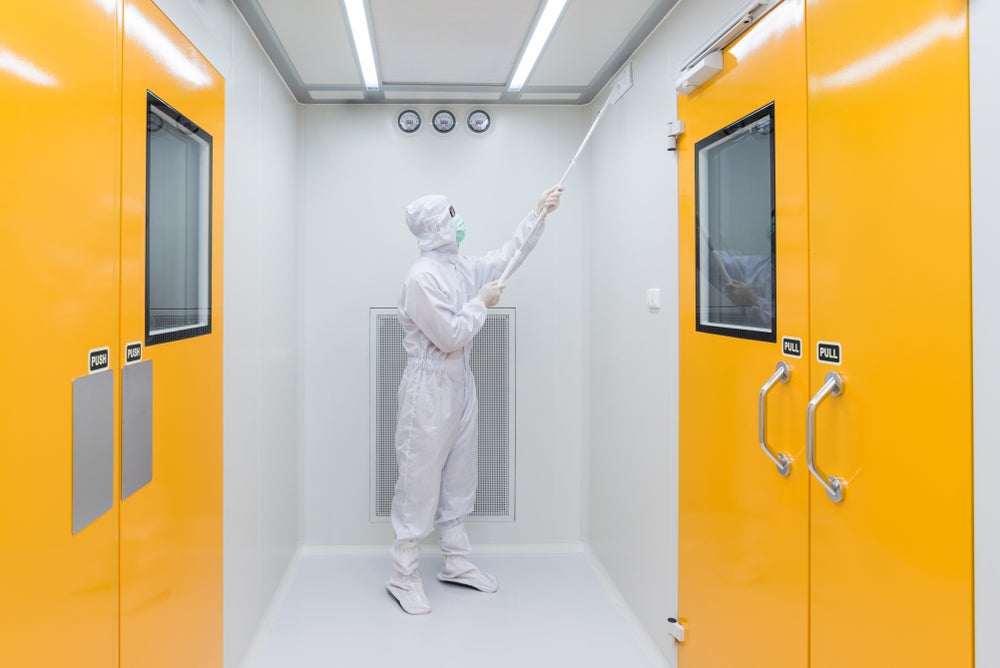
Today’s cleanrooms use equipment and engineering to guarantee low contaminant levels in research and manufacturing facilities. Due to the necessity for minimal contamination, cleanroom technology is prevalent in the production of certain drugs, biologics and vaccines, and hospitals.
Researchers often use single-use consumables like containers, pipettes, and apparel to maintain a sterile environment. Maintaining a balance between minimising the risk of contamination and being environmentally friendly is a challenge. Yet with calls for safety and sustainability increasing in frequency and volume, developers are exploring initiatives to narrow the gap and design cleanrooms for now and the future.
Cleanroom personalisation as standard
To meet the particular needs of individual medical environments, cleanrooms are often custom designed to fit exact specifications. Each healthcare process varies. There is a range of different equipment and personnel that also changes depending upon the production stage. “These factors create different contamination control challenges and each cleanroom needs to be tailored for its intended use,” says Dr. Tim Sandle, Pharmaceutical Microbiologist and Contamination Control Expert.
However, certain cleanroom components remain consistent, such as ensuring constant air circulation through High-Efficiency Particulate Absorbing (HEPA) filters and controlling temperature and humidity rates. HEPA-filtered air, and air exchange rates that are far faster than non-cleanroom environments will decrease viral transmission.
“To truly understand the cleanroom workspace, the most important aspect is drawing up the process flow,” says Sandle. During this process, the cleanroom management, engineers and quality assurance personnel map the path that equipment, product and operators will take in the cleanroom. Established quality risk management tools like Hazard Analysis and Critical Control Points (HACCP) or Failure Modes and Effects Analysis (FMEA) can be used for this purpose.
Particle levels generated from equipment and people are important considerations in cleanroom design, both in terms of their overall concentration and the direction of air vectors in relation to more critical areas. For example, a pattern of particles generated in one locale may or may not be a problem depending on the air movement and overall clean-up time. The impact of adjacent areas is another key consideration, especially how people and equipment are moved from lower-graded areas to higher-graded ones.
How well do you really know your competitors?
Access the most comprehensive Company Profiles on the market, powered by GlobalData. Save hours of research. Gain competitive edge.
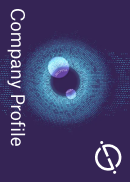
Thank you!
Your download email will arrive shortly
Not ready to buy yet? Download a free sample
We are confident about the unique quality of our Company Profiles. However, we want you to make the most beneficial decision for your business, so we offer a free sample that you can download by submitting the below form
By GlobalDataThe cleanroom design challenge
“The primary challenge within any cleanroom is people because they are the primary variable,” says Sandle. While consistency can be introduced through good gowning and controlling movements through training, people are the main source of contamination. “The main way to protect critical areas from people is through separative technology, such as the use of isolators,” Sandals continues. Isolators cut out personnel interaction with the product.
“Cleanrooms need to be designed to achieve control as per the maximum occupancy under conditions when all equipment is operating,” adds Sandle. Any weaknesses present, such as the slowing down of air or eddying, need to be overcome. A further consideration is the heat generated from equipment, which can exert an adverse effect on the airflow. “This is one reason why my many attempts at computational fluid dynamics (CFD) modelling have been unsuccessful,” Sandle notes.
The Covid-19 pandemic has increased the demand for modular cleanrooms in the form of pop-up centres to enable more testing. Some established facilities have also expanded their operations more permanently by increasing the size and scale of their cleanroom operations. Modular cleanrooms also offer flexibility in design, which is important for small-scale or emerging technologies, such as biotechnology.
Making cleanrooms more sustainable
To improve design and create more sustainable cleanrooms, Building Information Modelling (BIM) software has enabled “better development and for different scenarios to be more accurately assessed”, Sandle relays. BIM covers geometry, spatial relationships, light analysis, geographic information, quantities and properties of building components.
Recycled materials for apparel, energy-efficient processes and systems and digital technologies are coming to the fore. Innovations to reduce stationary use and investments in stainless steel systems with larger capacities that replace single-use systems, decontamination via UV disinfection, and minimising the use of single-use plastics strive to bring eco-consciousness to cleanrooms.
The design and operation of motorised fan units is an important way of controlling cleanroom energy. Advances in microcomputing also allow motors to be dynamically self-adjusting, whereby the airflow adjusts to changes in pressure or to the filter loading. Air adjustment enables the motor to require less energy when the cleanroom is in the static state compared with its in-use state, Sandle details.
Cleanroom companies are also looking at construction materials and their overall carbon footprint. Many discarded cleanroom products can be recycled. Cleanroom garments, including coveralls, hoods, boot covers, hair nets and masks, can be collected, converted, and resold as bulk plastics or converted into eco-friendly consumer products.
Reducing risk
In a climate with growing cost concerns, the energy consumption of cleanrooms is high. Controlled environments consume around 25 times more energy than non-classified spaces in buildings, Sandle details. “Pharmaceutical companies are seeking to lower their costs in an economic climate of escalating energy costs, and this is the key driver,” says Sandle.
The cleanroom sector’s main focus in incorporating sustainability into its design, however, has been in assessing air change rates. “In some cases, these have been ‘over designed’ and have been set too high based on the nature of the operations,” says Sandle. “A more risk-centric approach, drawing on empirical data from particle count studies, can provide a steady and controlled process for decreasing the rate of air into a cleanroom,” Sandle continues.
Different design elements appear with dehumidification. “Data suggests that dehumidifying the outside air and combining it with return air leads to a reduction in energy consumption for both cooling and reheating processes,” says Sandle.
However, while this airflow can be modified, this must never be to the detriment of contamination control. In the planning stage, life cycle inventories can balance cost, safety and sustainability. These inventories refer to the “detailed descriptions of what it takes to produce products and the environmental impacts of these steps”, says Evan Griffing, Cleanroom Researcher and Principal Consultant at Environmental Clarity.
Based on what laundry operators have told Environmental Clarity, Griffing confirms, “We believe that the cleanrooms are motivated to consider sustainability.”