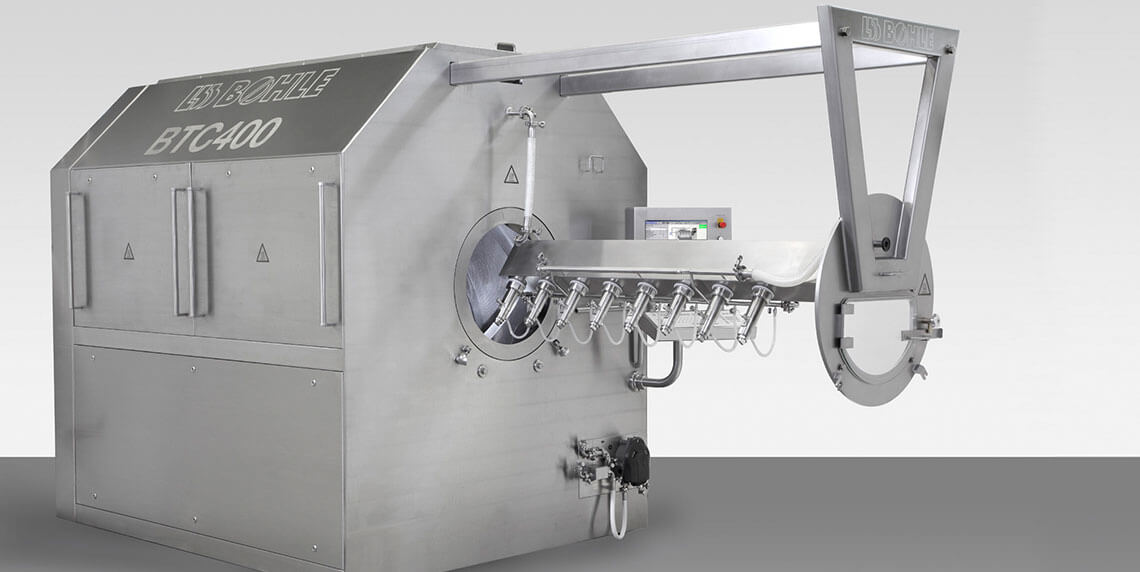
Nowadays, pharmaceutical film coating represents a significant process step in the pharmaceutical industry. Developed continuously in the last decades, coating technology originally derived from dragée pan processing. Most coating processes take place for drug stability improvement, drug release modification and taste masking. Patient compliance issues also play a crucial role, through more manageable identification due to an unusual colour, or swallowability improvement.
Active pharmaceutical ingredient (API) coating is also becoming increasingly significant, as it allows fixed-dose combinations, as well as the combination of incompatible drugs, facilitating classification of varying drug release properties through the addition of different coating layers. Formulations can consist of up to four coating layers, leading to lengthy processing times. Developing and manufacturing formulations coating uniformity is a perquisite and quality characteristic, as coated tablets must pass the test on the uniformity of dosage units according to the pharmacopoeias.
As a coating process consists of simultaneous spraying, mixing and drying processes, successful coating uniformity can only be accomplished with the selection of fitting parameters. To meet these demands, LB Bohle developed and refined its coated design in recent years.
Bohle Coating Technology comprises three unique design principles to ensure good coating uniformity.
Pan geometry for pharmaceutical film coating
With an L/D ratio >1, Bohle’s pan geometry provides a wide tablet bed surface, allowing the incorporation of a high number of spray guns.
In comparison to conventional pan geometries on the market, Bohle’s pharmaceutical film coating technology can cut process time by 40% as a result of greater throughput of coating suspension. Furthermore, the thinner tablet bed produces a minimum shear onto tablets, enabling the coating of even the most vulnerable tablets.
Patented helical baffles
LB Bohle’s patented helical baffles consist of two baffle layers, responsible for the continuous and homogenous axial mixing within the tablet bed. Coupled with this, drum rotation maintains radial mixing, guaranteeing a dead zone free tablet bed. Within a few minutes, a homogeneous mixture in the tablet bed can typically be achieved, and tablets do not experience any acceleration peaks due to constant tablet movement, significantly lessening tablet damage and twinning.
Airflow principle
Bohle Film Coaters air principle use the drying capacity where most required – in the tablet bed. Therefore, the drying capacity of inlet air is used most effectively without heating the additional coater inner parts. Inlet air coming from underneath the tablet bed is directly sucked through the rotating tablet bed into the exhaust air funnel. A further advantage to this setup is that the spray guns are not heated during coating, remaining cool. As a result, spray losses are reduced to a minimum, leading to coating efficiencies of less than 95%, especially beneficial for API coating processes.
On top of these unique features that make Bohle Coating Technology so successful, clean-in-place (CIP) systems can be fitted onto the coating machines. At high-pressure values, cleaning occurs with a cleaning lance, which effectively treats the coater following automated production.
LB Bohle provides coating equipment from lab scale to large production scale. Different configuration lines are offered to meet varying client requirements on all continents. Classical batch mode machine types and semi-continuous coaters are also available.
Download LB Bohle’s free White Paper to find out more on the company’s coating processes.