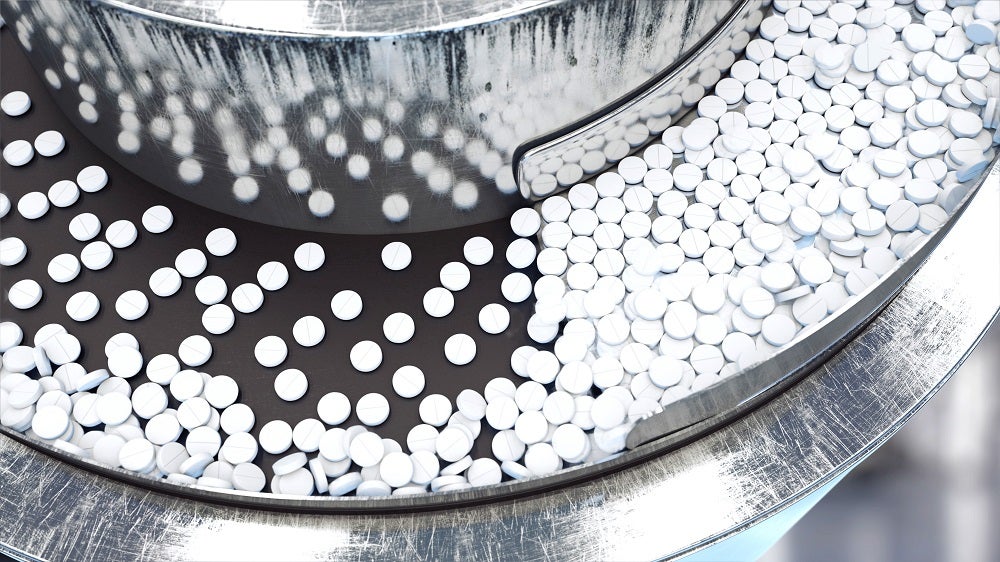
All evidence indicated that containment in facilities is in high demand and will be increasingly so in the future as the oncology pipeline and the use of cytotoxic drugs continues to grow. For pharmaceutical manufacturers and contract manufacturing organizations (CMOs) with containment capabilities, this likely means a distinct advantage over those without.
But not all manufacturers possess the space or capital to invest in multiple pieces of equipment to conduct safe, effective milling, and the associated high-value nature of small molecule API facilities will often involve manufacturing specialties that only a small minority of sites can offer. In fact, GlobalData observed that controlled substance manufacture and containment capabilities feature most strongly with larger organizations that can afford to develop or acquire these specialist capabilities. Dedicated manufacturers are investing heavily in these services, powered by client requirements.
As such, specialty small molecule API services are in high demand. For manufacturers big and small, competition is on the rise, but challenges with equipment footprint and expense remain. In a bid to overcome these hurdles, industry experts are turning to existing solutions and seeking ways to optimize performance, while shrinking costs and machinery mass.
A revolutionary development
For manufacturer of premium mills, Frewitt, perfecting the pharmaceutical milling process has been its mission since the company’s inception in 1946. Its most recent innovation has sought to reinvent the drum inverter process, providing operators with an effective handling and milling solution that overcomes some of the industry’s key hurdles: safety, footprint, and cost.
Traditional drum inverters are designed to transfer materials out of drums by fully inverting them to remove the contents, achieving various levels of containment. In the past, manufacturers would typically require two pieces of equipment for the handling and milling process.
Frewitt’s new Smart Inverter offers users a unique, three-in-one solution, providing lifting, handling and milling on the same machine, and therefore reducing the footprint and investment by half. This new generation of drum inverter enables the safe, ergonomic connection and disconnection of drums by a single operator. Compact in volume, it is an electrically powered solution with a lift raising the drum, rotating it into feed position, and proceeding directly to milling and discharging.
The milling head connects directly to the drums and a powerful torque rotates the head and up to 100-liter drums with ease. The vertical lift with a 300mm stroke also allows a wide range of drum sizes to be docked. Additionally, the option of Frelift (Frewitt’s mobile lifting column) enables users to discharge drums into a larger IBC, bag, or drum as per user need.
Milling mastered
According to Roy Housh, commercial director at Frewitt: “We have seen a growing trend to do away with manual loading, so we wanted to improve the machine loading process.
“The Smart Inverter took two years and several prototypes to design and create. It allows operators to deal with one piece of equipment, and for all functions to be controlled on a single HMI. It saves on m2/m3 and allows for any process suite to have more space for other equipment.
“It also allows for easy lifting and handling of drums so that human effort is eliminated. The three functions integrated into one machine – lifting, inverting, milling, have not existed together until now.”
Offering secure transfer of product into the milling chamber, the Smart Inverter is dust free, and with no physical lifting, assures the operator’s comfort and safety. Furthermore, the absence of human intervention makes the process as repetitive as possible. This all translates into a 50% gain on machine investment, footprint cost, maintenance costs, and handling and cleaning times.
According to Roy Housh: “At Frewitt we have mastered the milling process and are proud of this newly patented accomplishment that pushes the boundaries of safe powder handling and milling even further.”
To discover more about this revolution in milling, download the paper below.