Starting as a technology historically reserved for moisture or heat-sensitive products, roller compaction has evolved to become a widely used granulation technology with a broad range of applications. The dry granulate is either an intermediate product to be further processed into tablets, or it already represents the final bulk product to be packed in sachets, pouches, blister packs, plastic bottles, canisters, or used in the production of tablets and capsules.
Main reasons for granulation
The main purpose of dry granulation is to increase the bulk density of powders and increase the particle size to ensure a better flow of distributed material, which in turn results in better processability. In pharma, the goal is often to achieve a more uniform tablet. Granulated powder blends become more homogeneous, segregation is avoided, and the content uniformity increases. Further, granulation also reduces dusts and fines, especially for bulk products, resulting in little or no material wastage and low dust exposure.
Industries using roller compaction
Whenever granules of consistent and high product quality are required, variable gap roller compactors using sophisticated process controls are needed. While the pharmaceutical industry is still the key market with 95% of all compactors, Gerteis roller compactors can also be found manufacturing a wide range of products in the Food and Chemical industries (Figure 1).
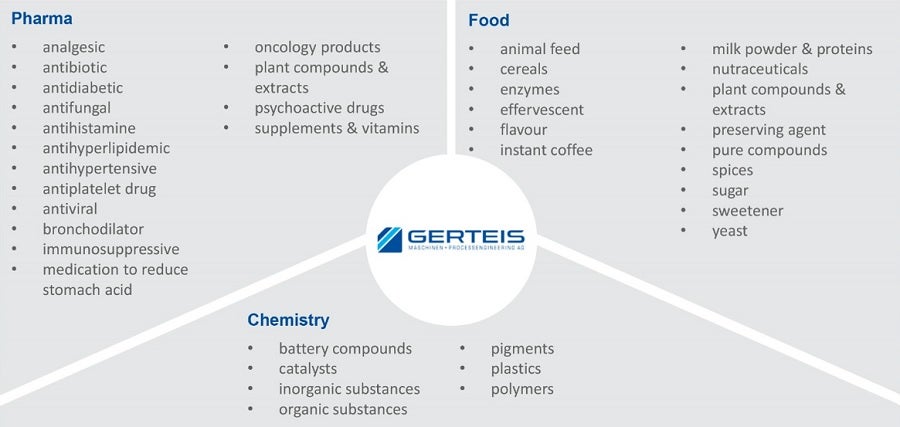
Application of dry granulation in pharma
The number of products being manufactured by Gerteis roller compactors continues to increase steadily as this granulation method has proven to be one of the most economical. It is continuous, has a relatively large throughput, requires little floor space, needs very little energy, and benefits from the absence of granulation liquids and drying equipment.
Roller compaction can be applied to a wide range of products. Many generic drugs are dry granulated, such as Metformin, Ibuprofen, antihypertensives and antibiotics. It is becoming more and more common, however, for proprietary products to be developed with dry granulation from the beginning. The range includes blockbusters such as Metformin but also orphan drugs like Bosentan.
Although roller compaction is a continuous manufacturing process suitable for both large and small batch sizes, almost all products are manufactured in batch format. The reason for this is that currently few products have been approved as a fully continuous manufacturing process. One example, Symdeko from Vertex, was approved in 2018 by the US FDA, having dry granulation integrated in a continuous manufacturing line. Additionally, Symdeko is a combination of two APIs used for the treatment of cystic fibrosis, demonstrating that candidates for roller compaction are not limited to single API products. Other examples of API combinations can be found within antihypertensive drugs such as Trandolapril & Verapamil or Valsartan & Hydrochlorothiazide (HTCZ).
The drug load for dry granulation formulations ranges from very high (>90% for Metformin or Ibuprofen) to very low (<1% for Cabergolin). For formulations with high drug loads, the properties of the API become crucial, and it is not always possible to achieve efficient compaction with such high drug loads. For very low drug loads, the challenge lies in the uniform distribution of the API throughout the whole blended batch.
Roller compaction can be used for both immediate and sustained-release formulations and can also be used in the manufacture of effervescent formulations in one blend without separating the carbonate salts and the acid components. This reduces the effort of manufacturing two separate batches of wet granulate to only one manufacturing step.
Even if a substance was originally developed as wet granulate, it is often possible to change the granulation method to dry granulation. Since this usually comes with registration changes, we recommend a business case calculation and a feasibility study as the basis for further decisions. Successful changes from wet to dry granulation have already been performed with Metformin, Ibuprofen or Triamteren & Hydrochlorothiazide (HTCZ). Table 1 gives an excerpt of APIs processed by roller compaction.
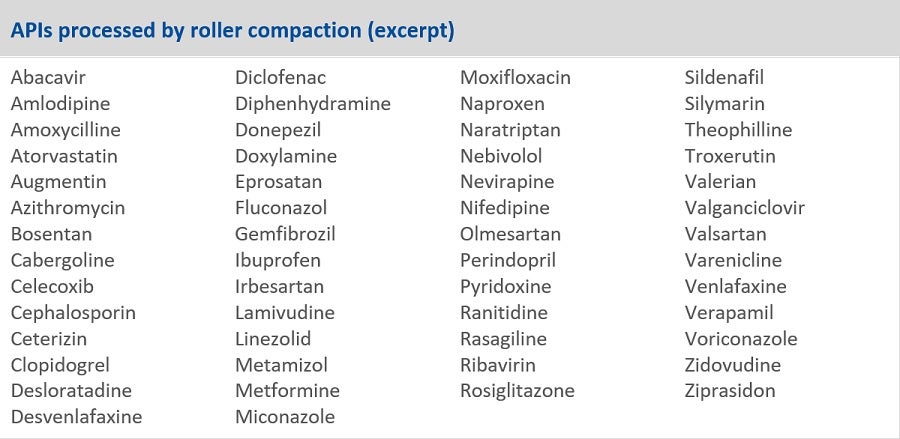
HPAPI
Driven by the need to contain and handle high-potent APIs (HPAPIs), roller compactors with different containment levels have been developed. Various leading CDMO companies such as Almac Pharma Services, Catalent Pharma Solutions, Fareva, Lonza and PCI Pharma Services have high-containment roller compactors from Gerteis in their manufacturing line. Containment levels of less than 0.1 µg/m³ (OEB 5 level) can be achieved using these machines.
Summary
The examples above show that roller compaction with Gerteis technology is used for a wide range of products and technologies and is not limited to moisture or heat-sensitive products. Various industries rely on consistent product quality and sophisticated process control. In the pharmaceutical industry, a large variety of formulations can be processed using roller compaction: batch or continuous, high-containment, proprietary or generic, blockbuster or orphan drug, high or low drug load, immediate or sustained release, API combinations, and many more. Roller compaction is a versatile, efficient method that saves time and money.
About Gerteis
GERTEIS Maschinen + Processengineering is a Swiss manufacturer of advanced high-quality roller compactors. GERTEIS® has set the standard since 1986 with its unique dry granulation technology. The company’s understanding of the dry granulation process, combined with patented roller compaction systems, makes GERTEIS the technology leader in the field of dry granulation.